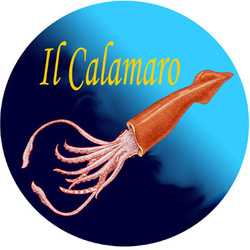
It's Memorial Day! We give thanks to all those who laid down their lives for this country, so that we might have the freedom to do wonderful things like participate in the International Submarine Races.
Since our last post, again, much has happened. One major milestone was writing and submitting our design report. Mrs. G helped tremendously with our report layout, and all team members worked on their respective sections. Everything was compiled at a "report writing party" where we worked pretty late into the night.
Another big milestone was getting the hull off the spindle. Step one was to cut the hatch out. That was scary...a really big commitment to our final design. But, armed with Rotozip, jigsaw and multi-tool, we were up to the challenge. Then all the foam had to be broken out. That was fun, but what a mess! Once we got the middle section out, the nose and tail sections came out in huge pieces. Our custom-made sub cart arrived (Thanks, Grandpa!) and was on hand when we slid the spindle out. Then we climbed inside and sanded.
We spent a lot of time tracking down a few items, but everything on our wish list arrived or was picked up. We made a notable field trip out to Deale, Maryland, to pick up supplies from Osprey Marine Composites. Their operation is quite impressive. Some other major things that were done: The acrylic windows were cut to size. The stabilizer fins were made. The dive planes, too, were made. All the propulsion system components were fabricated. We have a lot of assembly and testing to do. In other words, the adventure continues! Take a look at the photos below to get a sense of how things are shaping up.
Since our last post, again, much has happened. One major milestone was writing and submitting our design report. Mrs. G helped tremendously with our report layout, and all team members worked on their respective sections. Everything was compiled at a "report writing party" where we worked pretty late into the night.
Another big milestone was getting the hull off the spindle. Step one was to cut the hatch out. That was scary...a really big commitment to our final design. But, armed with Rotozip, jigsaw and multi-tool, we were up to the challenge. Then all the foam had to be broken out. That was fun, but what a mess! Once we got the middle section out, the nose and tail sections came out in huge pieces. Our custom-made sub cart arrived (Thanks, Grandpa!) and was on hand when we slid the spindle out. Then we climbed inside and sanded.
We spent a lot of time tracking down a few items, but everything on our wish list arrived or was picked up. We made a notable field trip out to Deale, Maryland, to pick up supplies from Osprey Marine Composites. Their operation is quite impressive. Some other major things that were done: The acrylic windows were cut to size. The stabilizer fins were made. The dive planes, too, were made. All the propulsion system components were fabricated. We have a lot of assembly and testing to do. In other words, the adventure continues! Take a look at the photos below to get a sense of how things are shaping up.
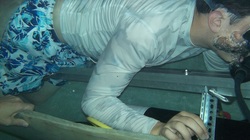
This photo shows Sam in the sub (hatch removed) when the sub was put in the water for the very first time at North Point High School Pool.
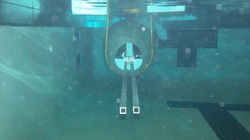
Here's a nice view of the tail of the sub with propulsion system (flaps removed) held temporarily in place by wedges of polystyrene.
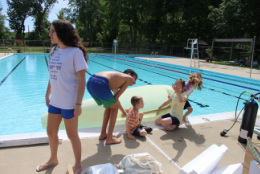
Here we are putting the hull (sans fins, windows, and propulsion system) in the water at the Moyaone Community Pool. Our junior assistants are keeping the hull tethered.
The hull is made from 5 layers of 10 oz fiberglass cloth and epoxy resin. In a few weeks it will be painted.
The hull is made from 5 layers of 10 oz fiberglass cloth and epoxy resin. In a few weeks it will be painted.
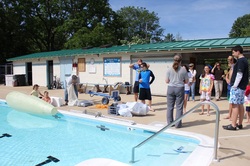
Everybody assembled on deck for the test briefing.
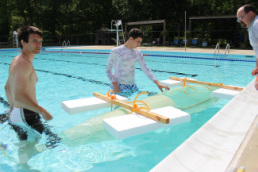
Our pilots get the hull submerged. They're also getting the idea of what the water temperature at ISR will be like. Here at the Moyaone Community Pool, the water temperature was 71F, about 6 degrees warmer than we expect it to be at David Taylor Model Basin. Brrrr.
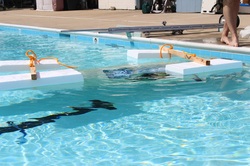
Look closely: Sam is in! The propulsion system is on the deck waiting to be inserted.
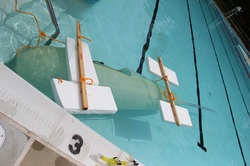
Here you get a good look at the propulsion drive shafts sticking out the tail of the sub. Our next batch of photo updates should show the propulsion system with the flappers on.
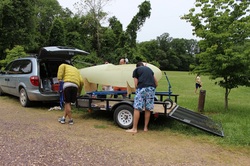
The trailer and the ground transportation cart. Grandpa Carts designed and built the cart using a standard hand cart as his starting point. The trailer in on loan for the duration of this project from his neighbor Doug, a retired Coastie.